"We’re proud to be significantly involved with our long-term customer in expanding battery expertise for the German market. We know the industry, we know how to implement large projects, and we bring experience to the table in programming and automating delicate battery assembly processes. Despite the challenges we’ve faced, the system is now in the test phase. This isn't just a milestone, for us personally, it also represents another important step along the road to expanding e-mobility."
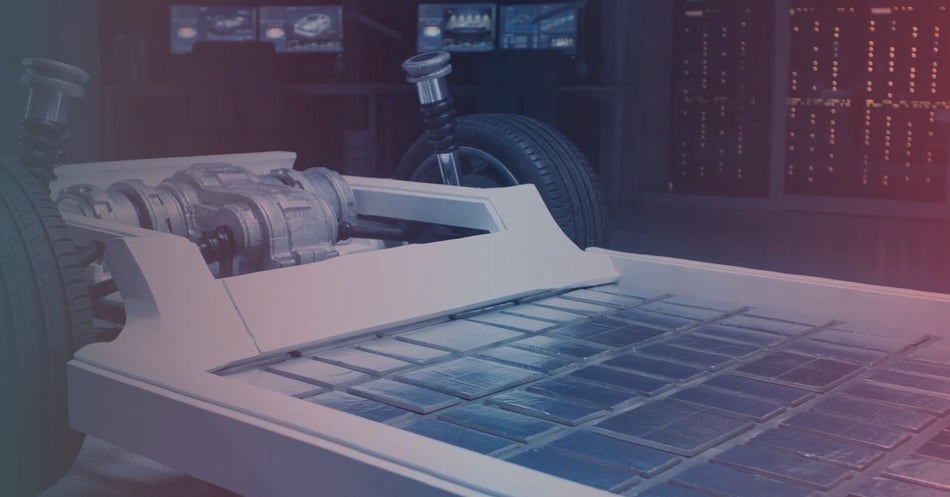
As a result of the ongoing mobility and energy transition, electromobility is rapidly gaining momentum. German automotive manufacturers, in particular, are increasingly focusing on expanding their battery expertise to keep pace with the dominant Asian market. In this dynamic environment, VESCON Automation is undertaking a complete electrical engineering project for a state-of-the-art battery assembly line at a leading Bavarian automotive manufacturer.
Markt
Market overview
- The market for battery cells is expected to grow from €20 billion in 2020 to €550 billion by 2030.
- 86% of this market is for mobility applications.
- Market share in battery plant manufacturing: Asia 92%, Europe is currently at 8%.
Source: Study by VDMA and Porsche Consulting
It's crucially important to expand battery assembly capabilities in order to cater to the growing electric vehicle market alongside traditional gasoline and diesel vehicles. A key area for this is electrical automation technology.
"We’ve been building our expertise in this area for years at SCIO, and partnered with OEMs from the very beginning to move the German sector forward together," emphasized Antonio Cavotta, Managing Director of VESCON Automation.
We’re currently involved in an exciting milestone project for a leading Bavarian automotive manufacturer.
The project
The project involves carrying out complete electrical engineering work on a highly automated assembly line for the battery assembly systems of two new electric models for the customer. To be more specific, it involves the system fully assembling the battery trays:
Our built-in conveyor technology transports the tray on a workpiece carrier from station to station. At each station, the battery system, which consists of individual modules and connections as well as a cooling system, is assembled step by step automatically. After assembly, the lid is glued on, and a control unit is installed to act as an interface to the vehicle.
The dimensions:
64
Robots
25
9
3
32
Process stations
9
4
Control system
The challenges
Controlling the systems for battery assembly is extremely demanding and requires exceptional precision and work needs to be carried out to the highest possible standards at our end. Experience in programming and meticulously executing processes is crucial. The important processes in battery assembly are as follows:
- Screwing processes
- Gluing processes
- Joining processes
- Monitoring processes
- Measurement processes (e.g., insulation measurements)
- Safety processes
From a technological standpoint, the modules must be precisely positioned and connected to ensure that they perform at their best and last as long as possible. This also requires the use of extremely precise robots and continuous adjustments during the process. Safety is the top priority, as lithium-ion batteries can easily catch fire. Another issue is that there aren’t any established standards for these kinds of systems at the moment.
In this article, we take a deep dive into additional challenges that battery assembly can pose, based on one of our projects.
Our solution
Precision & safety:
Each station communicates with an overarching monitoring system and is checked for OK release. If tested NOK (not OK), the battery tray is immediately removed from the system and reworked – including the most precise documentation.
Battery assembly systems, Made in Germany:
Our main goal is to establish efficient standards for automation and control technology in battery assembly. Our customer benefits from our many years of experience in large automotive projects and the fact that our engineering, programming and electrical engineering teams work together extremely closely.
Beyond the project:
Our teams’ shared standards and synergies mean that we've also been able to set up another assembly line at the customer's site in China at the same time.
Miroslav Jakovljevic, Project manager:
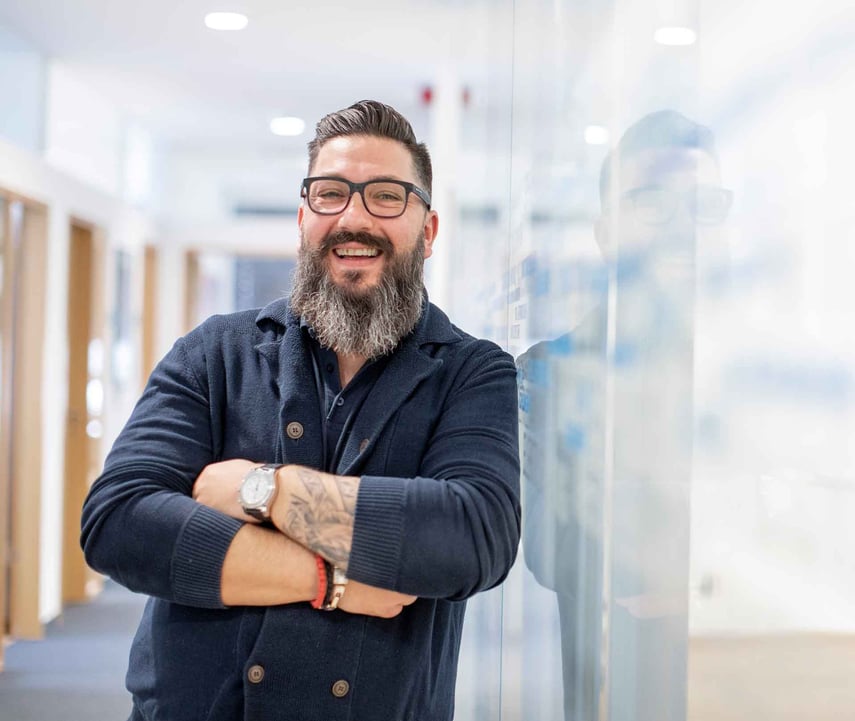
Find all services and information about VESCON Automation here.