Ensuring optimal plant reliability via Predictive Maintenance
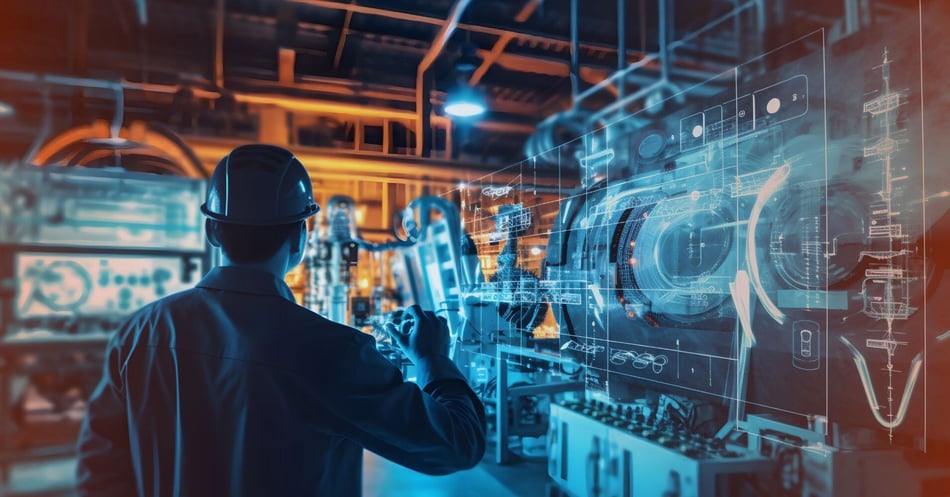
Predictive Maintenance isn't just a method for proactively maintaining your plants—it's a strategic opportunity to increase plant availability, significantly cut costs, and help define sustainability goals. In a current project focusing on air filter systems, the AUTKOM team is collaborating closely with a leading company in the mechanical engineering industry to drive this advanced technology forward.
When it comes to our mechanical engineering partners, we often see information flowing in one direction: from the maintenance system to the facility. In this case, rigid maintenance schedules and reactive approaches are the order of the day, for example, when a malfunction occurs.
But what if the facility proactively provides us with data and alerts us when something's amiss? And what if we could carry out inspections remotely?
This is precisely the principle of Predictive Maintenance that we're aiming to focus on with our customer (an air filter system manufacturer):
In companies such as foundries and paint shops, air filters play a crucial role in safety and efficiency. Using filters improperly, whether that’s due to excessively high temperatures or infrequent changes, may not only lead to spiraling costs, the safety of the entire system is put in jeopardy as well. If the filter fails, the foundry work must come to a halt! This is why we're working with our customer to develop an intelligent remote service system that keeps these risks to a minimum as part of predictive maintenance.
The race for data has begun
"Last year, we developed a new concept to remotely maintain air filters and successfully tested it with our customer. It was a challenging task, akin to open-heart surgery, as we tested it as the systems were running. Our expertise ensured that everything went smoothly, and we're poised for the first major pilot project," said Boris Vaisman, Automation Engineering Designer at AUTKOM.
The concept opens up valuable opportunities for our customers:
Plant damage can be tracked and traced
The data we collect pinpoint causes of errors, such as mistakes in the operational or planning phases, and can improve your system availability by up to 15%.
Smart maintenance
Data-driven maintenance reduces maintenance costs up to 25%, schedules downtimes, and extends the lifespan of your plants.
Saving on resources
Our remote access saves CO2 and makes work simple, both for you as customers, and for the service team.
Long-term monitoring
We identify trends and optimize systems by monitoring systems over the long term.
Install upgrades without any downtime
Systems can be retrofitted without any interruptions, for example, when collecting data.
"In collaboration with our SCIO subsidiary VESCON Systemtechnik, we're enhancing our system during the pilot phase by integrating their traceability and PDL software HIBERION. This robust system, which will be further enhanced with AI functionalities, is an ideal interface between plant operators and filters. It allows us to collect the data we need, identify anomalies using data analysis and AI algorithms, and plan maintenance needs with exceptional accuracy. Our goal is to create an intelligent plug-and-play solution that raises support to a new level and actively supports our customers as they work towards implementing sustainable practices", said Jens Koch, Head of Sales at AUTKOM.
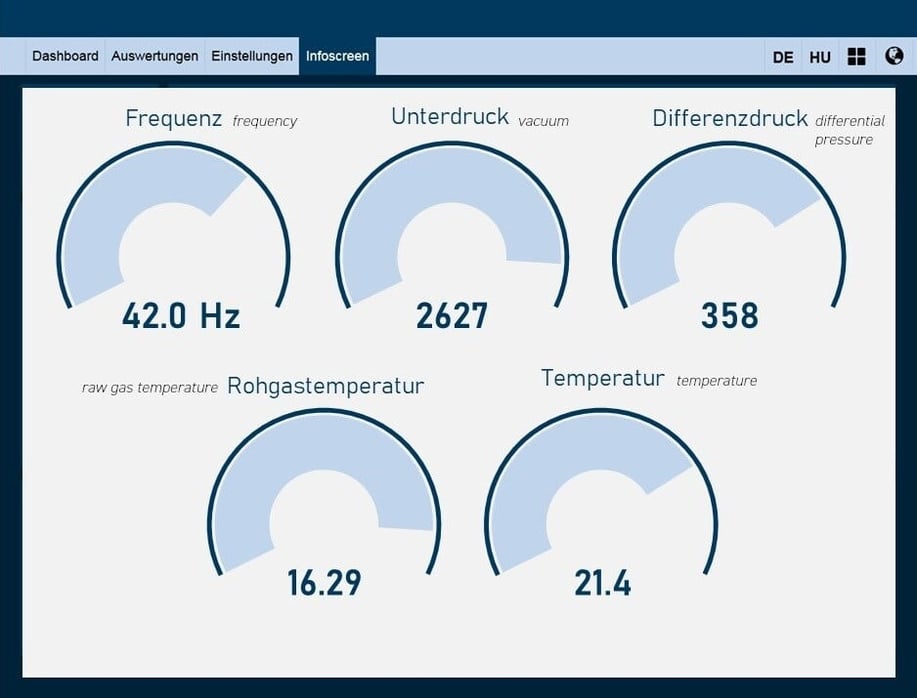
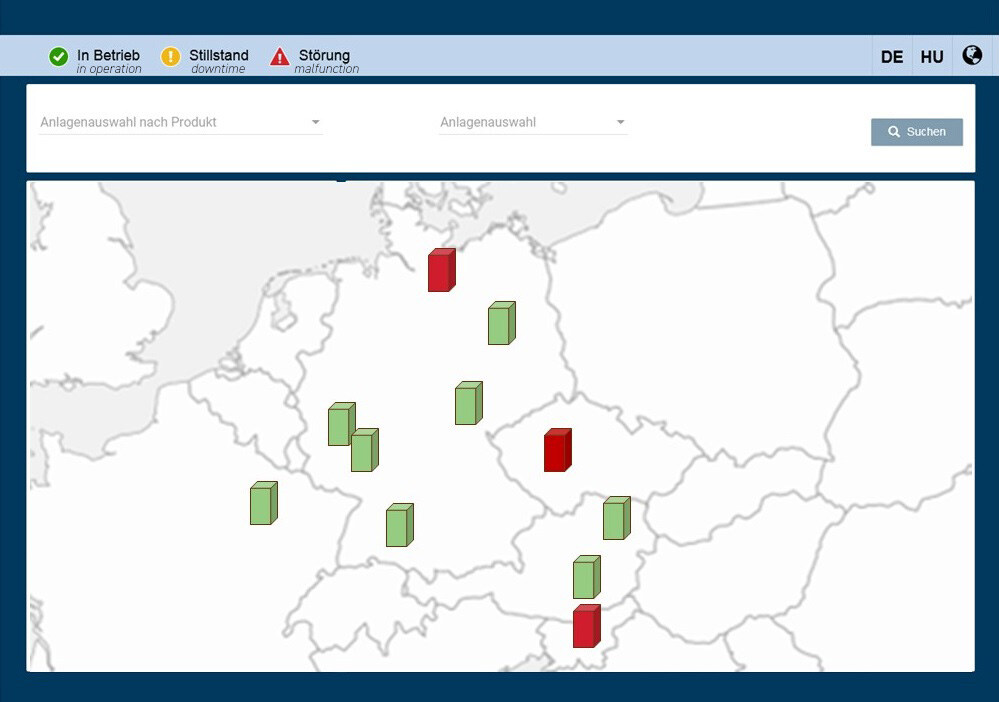
For more insights into Smart Production with HIBERION, click here.
How we provide “sustainable” support with predictive maintenance:
Our concept shows that we’re aiming to go beyond run-of-the-mill first-level support. It makes it much easier to collect data, and enables customers to utilize this data when they’re generating their reports on sustainability. This is becoming increasingly important, whether that’s due to regulatory requirements, or the growing pressure from the public and interest groups.
What other high potential areas could be tapped into as a result?
Imagine the foundries where our customer's air filters are used, leveraging the data we provide as a basis for specific goals and actions to improve their own environmental footprint. The company is able to analyze filter efficiency, pollutant emissions, and other relevant parameters to identify areas for optimization, and adapt its processes accordingly.
All in all, the year 2024 marks the beginning of an exciting new chapter for us: by introducing HIBERION as part of our pilot project, we're setting a milestone on the path to predictive and sustainable maintenance. After a successful pilot phase, we aim to implement the system in all of our customer's facilities.
Interested in joining forces with an experienced partner to pave the way toward a greener and more transparent future? Learn more about our services here.